Reviews
How to Build a Safer Manufacturing Facility: Systems, Tools, and Protocols
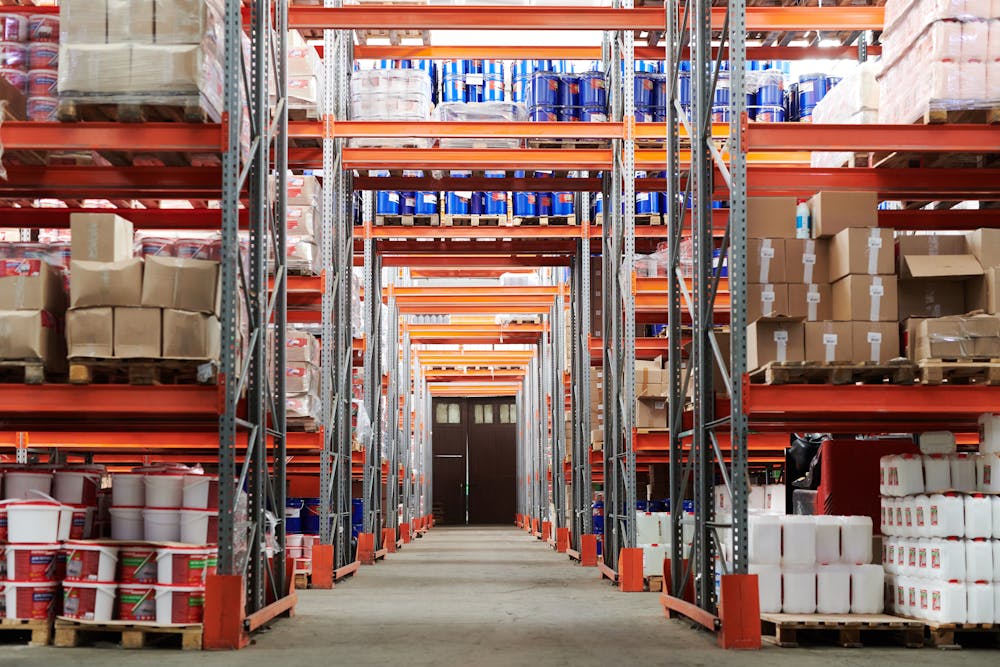
Manufacturing and industrial operations are the backbone of countless economies, providing essential goods, infrastructure, and services. However, the nature of these environments inherently carries risks—ranging from mechanical hazards to chemical exposure and environmental threats. Therefore, implementing and maintaining proper safety protocols is not just a regulatory requirement; it is a moral and operational imperative.
A comprehensive safety strategy helps protect workers, minimize downtime, preserve equipment, and improve productivity. This article outlines key safety protocols for manufacturing and industrial facilities, explores specific concerns like fire suppression systems, and emphasizes the importance of cultivating a proactive safety culture.
1. Conducting Thorough Risk Assessments
Proactive Identification of Hazards
A successful safety program begins with a thorough hazard identification process. Facilities must regularly inspect all operational areas, from production lines and material storage to chemical labs and shipping docks. Risk assessments should analyze:
- Physical hazards (e.g., machinery, noise, heat)
- Chemical risks (e.g., flammable liquids, corrosive materials)
- Ergonomic hazards (e.g., repetitive motions, poor posture)
- Biological threats (e.g., mold, bacteria in food facilities)
- Environmental concerns (e.g., poor lighting, ventilation)
These assessments should be updated routinely and after every incident or significant operational change.
Job Safety Analysis (JSA)
For higher-risk tasks, perform JSAs to break down each step of a job, identify potential hazards, and determine safer procedures. JSAs promote situational awareness and can be used during onboarding or regular training sessions.
2. Safety Training and Competency Development
New Employee Orientation
All new hires should undergo a comprehensive orientation program that covers workplace hazards, emergency procedures, and the proper use of personal protective equipment (PPE). Introduce the facility’s safety philosophy and expectations early.
Ongoing and Specialized Training
Annual refresher courses, toolbox talks, and simulation-based learning help employees stay up to date. Workers should also receive role-specific training, such as:
- Forklift safety certifications
- Confined space entry procedures
- Lockout/tagout (LOTO) compliance
- Fall protection for elevated work
Supervisors and safety officers must also be trained in incident investigation, first response, and regulatory compliance.
3. Personal Protective Equipment (PPE) Standards
Assessing PPE Requirements
Depending on the nature of the job, PPE might include:
- Eye protection (safety glasses, goggles)
- Respiratory protection (N95 masks, SCBA units)
- Protective clothing (flame-resistant uniforms, lab coats)
- Hearing protection (earplugs, earmuffs)
- Footwear (steel-toe boots, anti-static shoes)
Maintenance and Accessibility
PPE must be maintained in good condition, stored properly, and easily accessible. Employees should be trained on the correct donning, doffing, and care of their protective equipment.
4. Engineering and Environmental Controls
Machine Safeguarding and Automation
Machinery should be equipped with physical guards, emergency stop buttons, and interlocking devices. Where possible, automation and robotics should be used to reduce exposure to dangerous tasks, such as welding, material handling, or chemical dispensing.
Ventilation and Air Quality
Proper HVAC systems are essential to reduce exposure to fumes, dust, and airborne contaminants. Facilities that use solvents or flammable gases must include local exhaust ventilation and gas detection systems.
Lighting and Ergonomics
Adequate lighting in work areas prevents slips and errors, while ergonomic workstation design reduces strain injuries. Adjustable workstations, anti-fatigue mats, and mechanical lifting aids contribute to worker comfort and safety.
5. Safe Material Handling and Storage
Labeling and Classification
All hazardous materials must be clearly labeled according to local or international standards (e.g., OSHA’s HCS or the Globally Harmonized System). Safety Data Sheets (SDS) should be accessible at all times.
Storage Guidelines
Segregate incompatible substances (e.g., acids and bases), store flammables in approved cabinets, and ensure proper shelving, racking, and containment systems are used. Materials should not be stored too high or too close to heat sources.
Manual Handling Protocols
Provide carts, lifts, and hoists to reduce strain. Train workers in proper lifting techniques and encourage reporting of musculoskeletal issues early.
6. Fire Safety and Suppression Systems
Fire safety in industrial settings is critical due to the presence of flammable materials, electrical equipment, and high-temperature processes. Prevention is the first line of defense, but when fire risks emerge, turning to experts for fire suppression system installation becomes essential..
Types of Fire Suppression Systems
- Wet Pipe Sprinkler Systems
Always filled with water and activate quickly. These are suitable for most indoor manufacturing spaces unless freezing is a concern. - Dry Pipe Sprinkler Systems
Filled with pressurized air or nitrogen and used in unheated areas (e.g., loading docks, outdoor warehouses) to prevent pipe freezing. - Pre-Action Systems
Require two triggers (e.g., smoke detection and heat) before releasing water. Ideal for high-value areas where accidental discharge could cause damage. - Foam-Based Systems
Effective in facilities handling petroleum products or hazardous chemicals. Foam smothers flammable liquids by creating a seal over the surface. - Gaseous Suppression Systems
Use clean agents (e.g., FM-200, CO₂, Novec 1230) to suppress fire without damaging electronics or sensitive equipment—perfect for control rooms, server centers, and laboratories. - Manual Fire Suppression Tools
Fire extinguishers, fire blankets, and hose reels must be regularly inspected and placed in accessible, well-marked areas throughout the facility.
Regular Testing and Maintenance
All suppression systems should be inspected monthly and tested according to NFPA or local fire authority guidelines. Fire drills and alarm response tests should also be integrated into the training calendar.
7. Emergency Response and Incident Management
Emergency Preparedness Plans
An emergency action plan (EAP) should include evacuation routes, shelter-in-place protocols, communication strategies, and roles for designated safety wardens. Facilities should also consider natural disaster responses depending on regional threats (e.g., earthquakes, floods, hurricanes).
First Aid and Medical Preparedness
Ensure first aid stations are fully stocked and that a percentage of employees are trained in CPR, AED use, and trauma care. Large sites may benefit from having an on-site clinic or paramedic support.
Incident Investigation and Reporting
When an incident occurs, immediate steps should be taken to secure the area, provide aid, and begin documentation. A root cause analysis (RCA) must follow, with corrective and preventive actions tracked until closure.
8. Regulatory Compliance and Auditing
Compliance with national and international safety regulations is non-negotiable. Key standards include:
- OSHA (Occupational Safety and Health Administration – U.S.)
- ISO 45001 (Occupational health and safety management systems)
- NFPA (Fire protection standards)
- EPA or equivalent environmental safety guidelines
Facilities should schedule both internal and third-party audits to ensure compliance, spot deficiencies, and stay prepared for unannounced inspections.
9. Building a Proactive Safety Culture
Leadership Commitment
Safety must be championed from the top. Leaders should actively participate in safety meetings, allocate resources for safety initiatives, and recognize teams for maintaining a strong safety record.
Employee Engagement
Encourage workers to report hazards without fear of retaliation. Suggestion boxes, safety committees, and open-door policies foster transparency.
Continuous Improvement
Use metrics like Total Recordable Incident Rate (TRIR), near-miss reports, and audit scores to measure progress and identify trends. Leverage data analytics to forecast risk and improve training content.
Conclusion
Safety in manufacturing and industrial facilities requires more than a checklist—it demands a coordinated, evolving strategy rooted in diligence, education, and culture. From risk assessments and machine safety to fire suppression systems and emergency preparedness, each layer plays a crucial role in protecting life and assets.
A well-implemented safety program not only keeps operations running smoothly but also demonstrates a company’s commitment to its workforce. In an industry where the smallest oversight can lead to devastating consequences, attention to safety isn’t just good practice—it’s a fundamental responsibility.
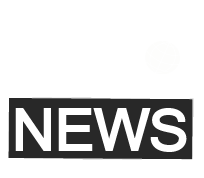
-
Legal7 days ago
Firefighters ambushed while responding to Idaho wildfire, at least 2 killed
-
US News1 week ago
Small meteorite fragment may have struck Georgia home
-
Legal1 week ago
Armed woman blocks traffic on freeway in Houston, Texas
-
Legal1 week ago
Washington Post journalist Thomas LeGro arrested for child porn possession
-
World7 days ago
Tropical Storm Barry forms in the Gulf, expected to make landfall in eastern Mexico
-
Legal5 days ago
Ovidio Guzmán, son of ‘El Chapo,’ to plead guilty in Chicago drug trafficking case
-
US News4 days ago
Massive explosions reported at fireworks site in Yolo County, California
-
Legal4 days ago
At least 4 injured in shooting at mall in Savannah, Georgia