Reviews
Maximizing Forklift Efficiency: Best Practices for Optimal Performance and Longevity
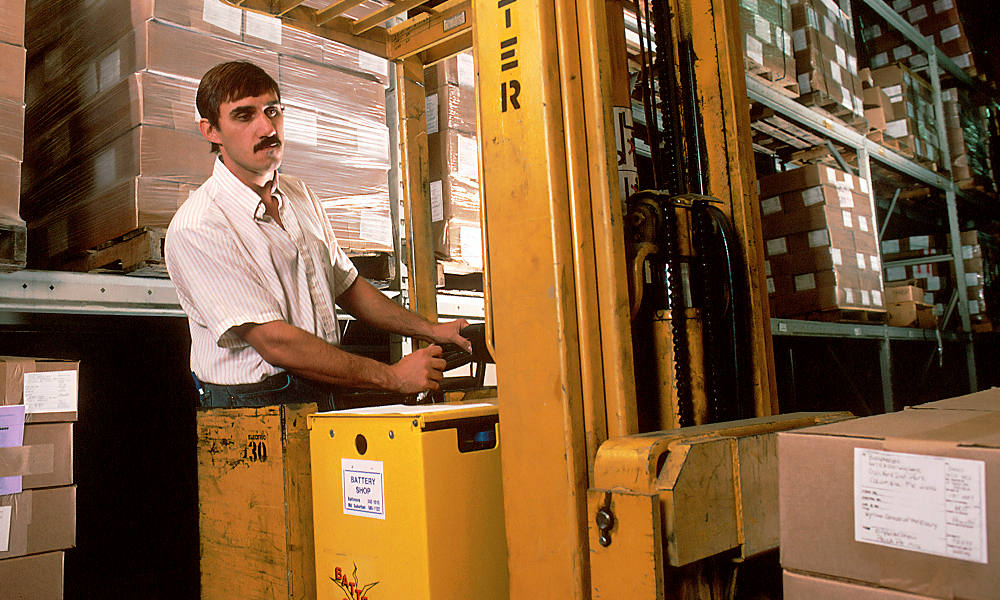
Forklifts are essential in warehouses, distribution centers, and construction sites. When used correctly, they enhance productivity, streamline operations, and improve workplace safety. However, inefficient forklift use leads to downtime, increased maintenance costs, and even safety hazards.
To get the most out of your forklift, it’s essential to focus on efficiency, proper maintenance, and the right attachments for the job. Below, we’ll break down the best strategies to maximize forklift performance while ensuring safety and longevity.
1. Perform Regular Maintenance and Inspections
A well-maintained forklift runs smoothly and reduces unexpected breakdowns. Routine maintenance isn’t just a recommendation—it’s necessary to keep your equipment operating at peak efficiency.
Before each shift, operators should conduct pre-use inspections. These quick checks help identify issues before they become major problems. Here’s what to look for:
- Fluid levels – Check oil, hydraulic fluid, and coolant.
- Tire condition – Look for wear, cracks, or low pressure (for pneumatic tires).
- Brakes and steering – Ensure responsive controls.
- Forks and mast – Inspect for bends, cracks, or misalignment.
- Warning lights and signals – Ensure they function properly for safety.
Scheduling routine servicing with a certified technician prevents costly repairs. Following the manufacturer’s maintenance schedule can extend the lifespan of your forklift significantly.
2. Train Operators for Maximum Productivity
A skilled operator makes all the difference in forklift efficiency. Investing in operator training reduces the risk of accidents, minimizes fuel consumption, and increases productivity.
Certified training programs teach operators:
- How to maneuver forklifts efficiently in tight spaces.
- The best load-handling techniques to prevent tipping.
- Proper braking and acceleration for fuel and battery efficiency.
Companies that implement regular refresher training see fewer workplace accidents and better forklift performance overall. According to OSHA, proper training can reduce forklift-related accidents by up to 70%.
3. Use the Right Forklift for the Job
Not all forklifts are the same. Choosing the right type for your operations makes a significant impact on efficiency. Consider these factors when selecting a forklift:
- Load capacity – Ensure the forklift can handle your heaviest loads.
- Environment – Electric forklifts are ideal for indoor use, while diesel or LPG forklifts are better for outdoor applications.
- Maneuverability – Smaller forklifts work better in tight warehouse spaces.
If your operations require frequent trailer loading, a fifth wheel forklift attachment can improve efficiency by making it easier to move semi-trailers. Attachments like side shifters and fork positioners also enhance material handling capabilities.
4. Optimize Warehouse Layout for Efficiency
A well-organized warehouse reduces forklift travel time and enhances workflow. If operators constantly navigate cluttered aisles or take long routes, productivity suffers.
Here’s how to improve warehouse layout for forklift efficiency:
- Clearly marked traffic lanes – Designate paths for forklifts to reduce congestion.
- Strategic storage placement – Place high-demand items closer to loading docks.
- Adequate turning space – Ensure forklifts have room to maneuver without obstruction.
By optimizing warehouse design, you minimize unnecessary movements, saving fuel, battery power, and time.
5. Reduce Downtime with Proper Battery and Fuel Management
Forklifts that rely on batteries or fuel require efficient energy management. Poor handling of fuel or batteries leads to frequent refueling, shortened battery life, and unnecessary downtime.
For electric forklifts:
- Charge batteries only when necessary to prevent overcharging.
- Keep water levels in lead-acid batteries at recommended levels.
- Store batteries in a cool, dry place to extend their lifespan.
For fuel-powered forklifts:
- Avoid unnecessary idling to conserve fuel.
- Perform regular engine maintenance to improve fuel efficiency.
- Use high-quality fuel to prevent engine buildup and wear.
Proper energy management ensures that forklifts stay operational throughout shifts with minimal interruptions.
6. Implement Safety Practices to Prevent Damage and Accidents
Accidents not only threaten worker safety but also lead to expensive equipment repairs and downtime. A few proactive safety measures can prevent mishaps and protect your investment.
- Enforce speed limits – High speeds increase the risk of tipping and collisions.
- Secure loads properly – Prevent imbalanced or overhanging loads that can fall.
- Monitor visibility – Ensure operators have clear sightlines, and use mirrors or cameras in blind spots.
When operators follow strict safety protocols, forklifts remain in good condition longer, and workplace injuries are reduced.
Conclusion
A forklift is more than just a piece of equipment—it’s a key player in warehouse and industrial operations. By conducting regular maintenance, training operators, choosing the right equipment, optimizing warehouse layouts, and managing energy use properly, businesses can maximize forklift efficiency while minimizing costs.
With the right approach, your forklift will run at peak performance for years to come, reducing downtime and improving overall productivity.
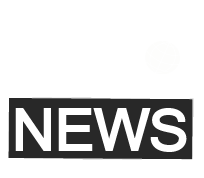
-
Breaking News3 days ago
Tsunami alerts for Pacific, including U.S. West Coast and Hawaii, after Russia quake
-
Legal7 days ago
11 people stabbed at Walmart in Traverse City, Michigan
-
Legal4 days ago
5 killed, including NYPD officer and the suspect, in Midtown Manhattan shooting
-
Business1 week ago
Starlink experiences widespread outage in U.S. and other countries
-
Legal6 days ago
Couple killed while hiking with daughters at Arkansas state park
-
World2 days ago
Over 20 injured after amusement ride collapses in Saudi Arabia
-
US News5 days ago
Small plane crashes into car in southern Florida, 7 hospitalized
-
Health4 days ago
Cambodia reports 14th human H5N1 bird flu infection in 2025